Enamel Industry Modern Transformation and Development of Traditional Craftsmanship
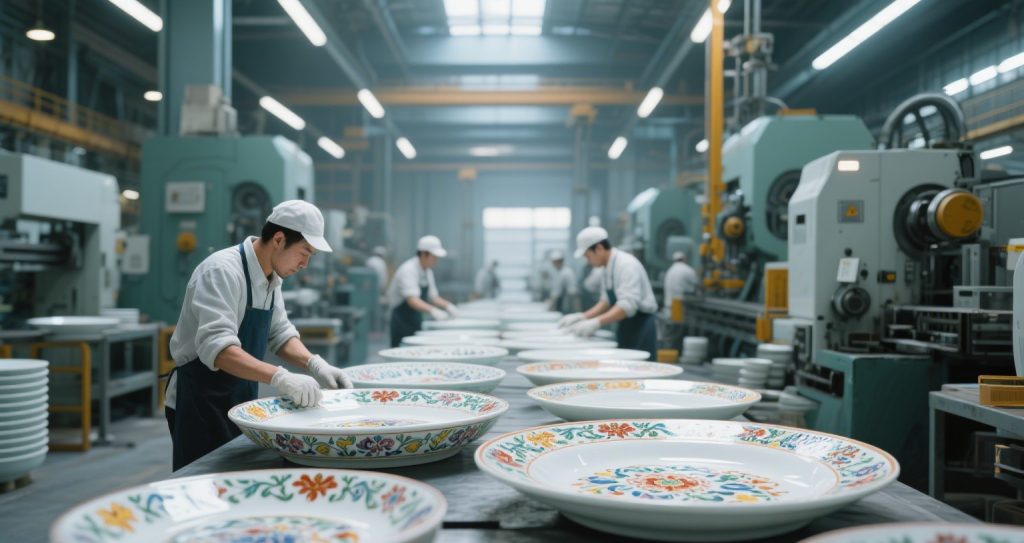
Introduction
Enamel, a unique composite material combining inorganic vitreous materials with a metal substrate, integrates the strength of metal and the aesthetics and corrosion resistance of glass, holding a significant position in human life and industrial production. From its early days as an exquisite handicraft to its widespread application in construction, home furnishings, industrial equipment, and numerous other fields today, the enamel industry has undergone a long developmental journey, continuously adapting to era needs and evolving and innovating in technological processes, product applications, and market landscapes.
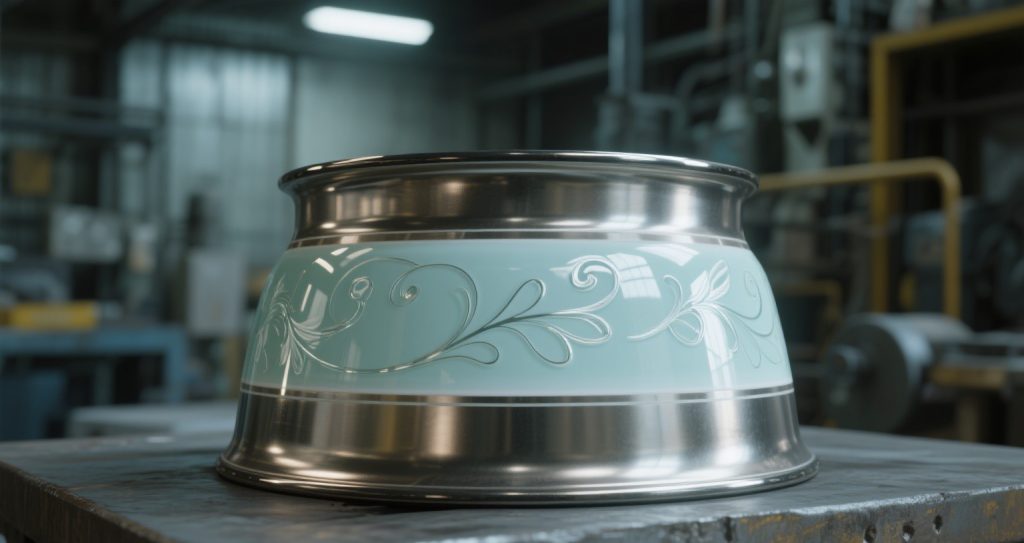
Definition and Historical Origin of Enamel
Enamel, also known as faience, is a composite material formed by fusing inorganic vitreous materials onto a base metal through melting and firmly bonding them together. Its history is long-standing: in the 6th century, European cloisonné enamel, champlevé enamel, bas-relief enamel, translucent enamel, and painted enamel emerged successively. In China, enamel craftsmanship began to develop in the 8th century, matured by the late 14th century, and reached particular prominence during the Jingtai period (mid-15th century) of the Ming Dynasty, giving rise to the name “Cloisonné.” In the early 19th century, cast iron enamel was developed in Europe, laying the foundation for enamel’s transition from handicrafts to daily necessities, though its application was limited by backward casting technology at the time. In the mid-19th century, with the vigorous development of various industries, steel plate enamel rose, inaugurating a new era of modern enamel. From the late 19th century to the first half of the 20th century, the successful research and development of enamels with different properties, the widespread application of steel plates and other metal materials, and the continuous updating of refractory materials, kilns, and enameling technologies greatly promoted the rapid development of the enamel industry.
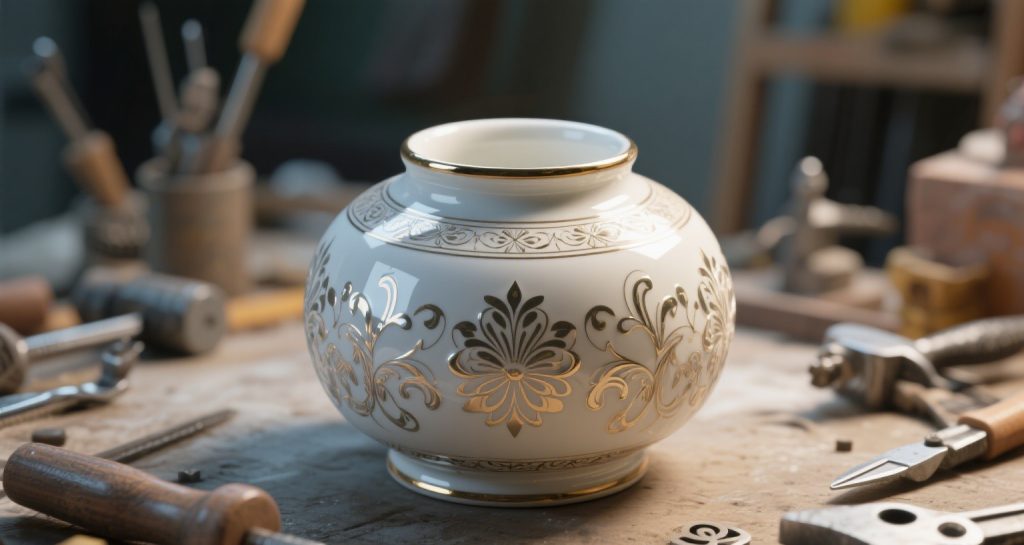
Detailed Explanation of Enamel Production Processes
- Raw Material Preparation
Selection of Metal Substrates: The first step in enamel production is carefully selecting suitable metal substrates, commonly including steel plates, cast iron, copper, aluminum, stainless steel, etc. Different metal substrates, due to variations in chemical composition, mechanical properties, and surface structure, are suitable for different types of enamel products. For example, steel plates are widely used in daily necessities and industrial equipment due to their good formability and weldability; cast iron is often used for manufacturing large industrial containers and bathroom products due to its high strength and wear resistance. Selection should comprehensively consider the product’s usage environment, performance requirements, and cost factors.
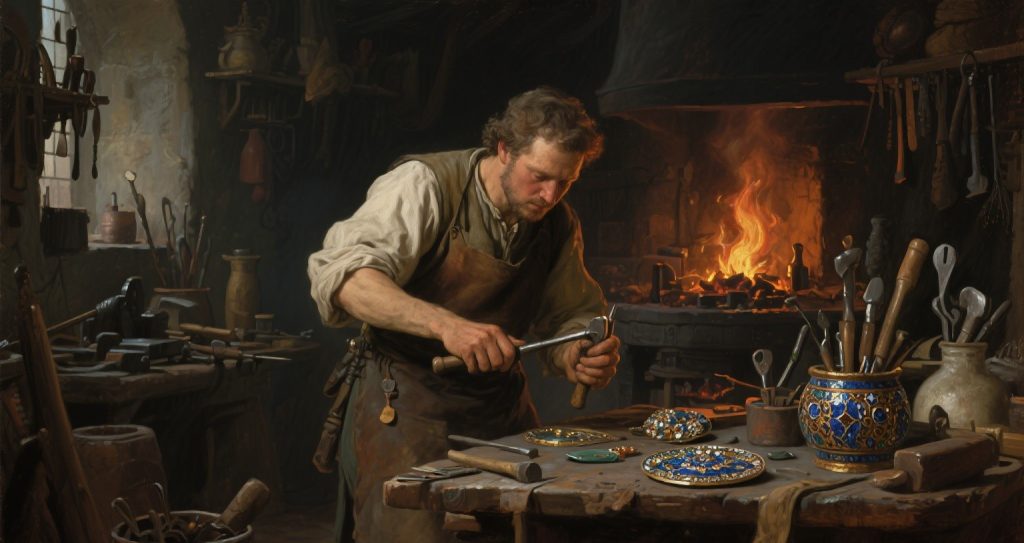
Enamel Preparation: Enamel is a key component of enamelware, a vitreous silicate or borosilicate coating applied to metal blanks. It mainly consists of a matrix (mostly silicates, boric oxide, aluminum oxide, and alkali metal oxides) and chemical raw materials (such as borax, sodium nitrate, soda ash, calcium carbonate, etc.). The chemical composition of the enamel is precisely determined according to the type of blank material and the product’s performance requirements. After accurately weighing various raw materials in specific proportions, they are fully mixed (either by dry mixing or adding 5-15% water to form pellets), then melted at high temperature in a tank kiln (mostly separate flame tank kilns in China), crucible kiln, or rotary furnace to achieve a certain degree of uniformity. Subsequently, they are quenched with water, air-cooled, or hot-pressed into thin sheets (0.6-1.5mm), and finally ground into dry enamel powder using a ball mill or air flow mill, or mixed with water to form an enamel slurry for standby.
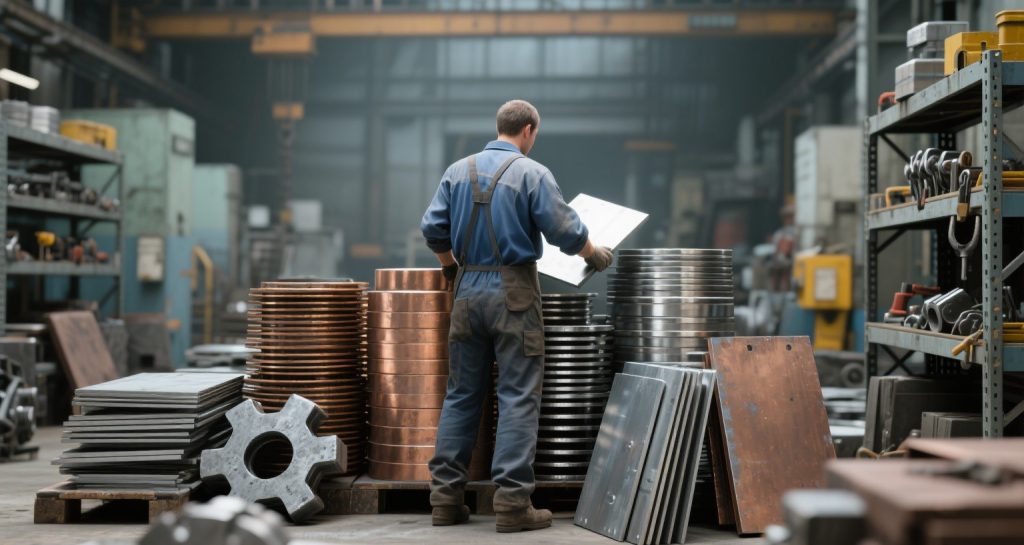
- Blank Preparation and Pretreatment
Before enameling, metal blanks require a series of strict pretreatment operations to ensure the firm bonding of enamel to the metal. First is surface cleaning: removing oil, rust, and impurities from the metal surface through degreasing, pickling, water washing, etc., to make the surface clean. Then, surface roughening treatment is carried out, such as sandblasting or shot blasting, to increase the roughness of the metal surface, expand the contact area between the enamel and the metal, and thus improve adhesion. For some blanks with complex shapes, pre-forming processing such as stamping or casting may also be required to give them a preliminary shape.
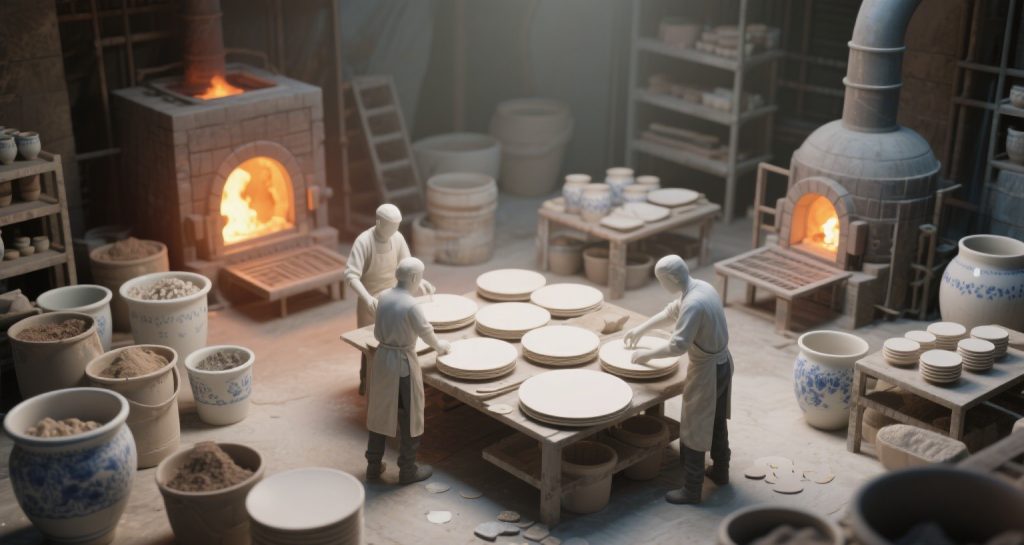
- Enameling Processes
- Traditional Enameling Methods:
- Dipping Method: The pretreated metal blank is completely immersed in the enamel slurry, allowing the surface to evenly adhere to a layer of slurry, then taken out to drain excess slurry. This method is simple to operate and suitable for regularly shaped, large-batch products, but may result in uneven coating for products with complex shapes.
- Pouring Method: The enamel slurry is directly poured into the mold of the metal blank, allowing it to evenly distribute on the blank’s surface, and demolded after the slurry solidifies. It is often used for producing large, thick-walled enamel products, such as enamel bathtubs.
- Spraying Method: The enamel slurry is atomized by a spray gun and sprayed onto the metal blank’s surface. By controlling the spray gun’s pressure, angle, and movement speed, uniform coating can be achieved, suitable for products with high surface quality requirements and complex shapes.
- Powder Sprinkling Method: Dry topcoat powder is directly sprinkled onto the hot ground coat, combining enameling and firing into one operation, especially suitable for enameling large cast iron parts (such as bathtubs, reaction kettles, etc.).
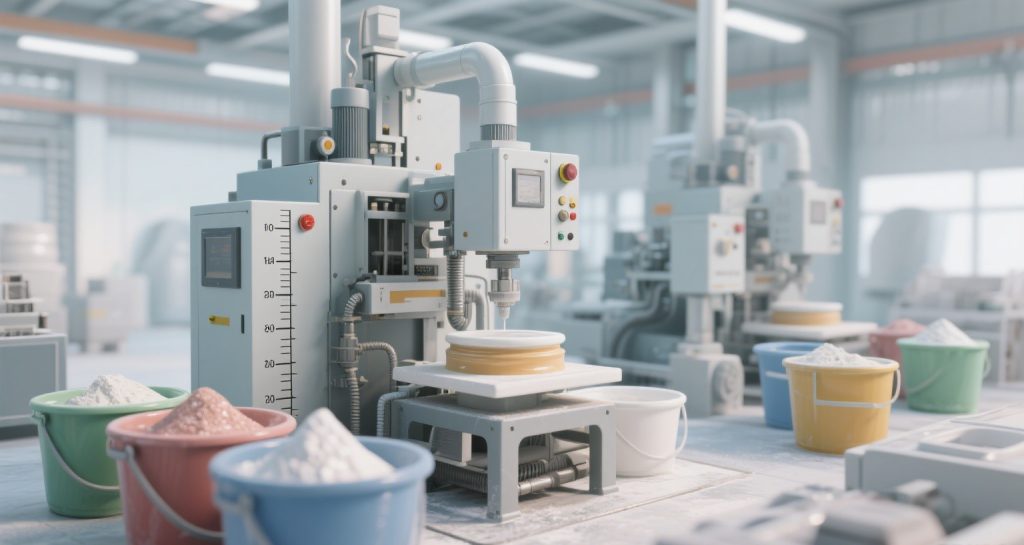
New Enameling Technologies: With technological development, new technologies such as electrostatic powder coating and electrophoretic enameling have gradually been applied. Electrostatic powder coating uses the principle of electrostatic adsorption to make charged dry enamel powder adsorb onto the grounded metal blank surface, forming a uniform coating. This method features uniform coating thickness, high quality, and effective reduction of dust pollution. Electrophoretic enameling deposits charged enamel slurry particles onto the metal blank surface under the action of an electric field, with advantages such as uniform coating, high production efficiency, and suitability for automated production, especially for products with extremely high requirements for coating quality and consistency.
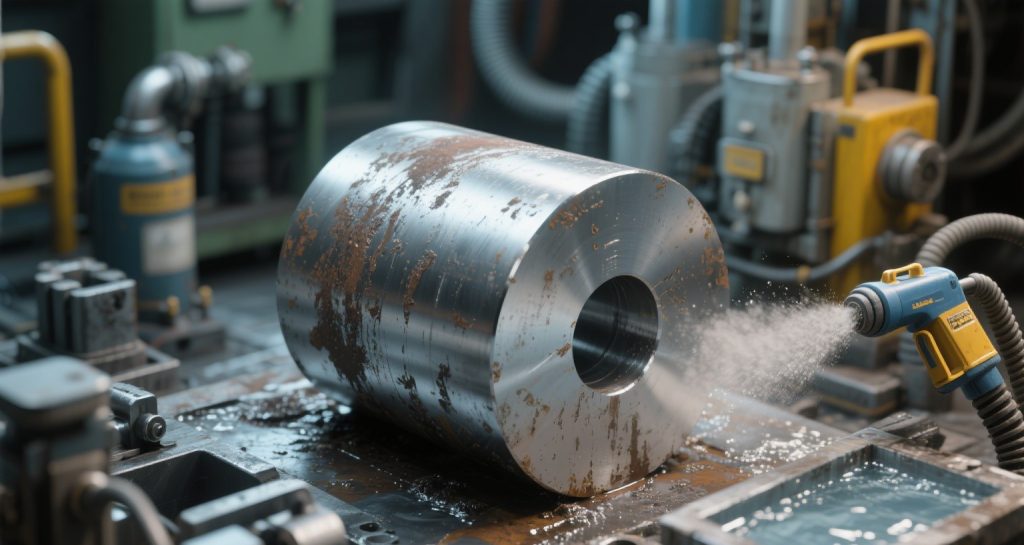
- Firing Process
The enameled blanks are fired in box furnaces, turntable furnaces, or tunnel furnaces. The borosilicate ground coat containing a bonding agent is fired at approximately 880-930°C, using an oxidizing atmosphere to form an iron oxide layer on the blank surface that facilitates good adhesion between the enamel layer and the steel. The firing temperature of the topcoat is slightly lower, for example, antimony opacified topcoat is 850-900°C, and titanium topcoat is 820-860°C. During firing, time and furnace atmosphere must be strictly controlled, as they directly affect the opacification effect, color brightness of the topcoat, and its tight bonding with the ground coat. For cast iron blanks using antimony and titanium enamels, atmosphere control is particularly critical, as slight deviations can affect product quality.
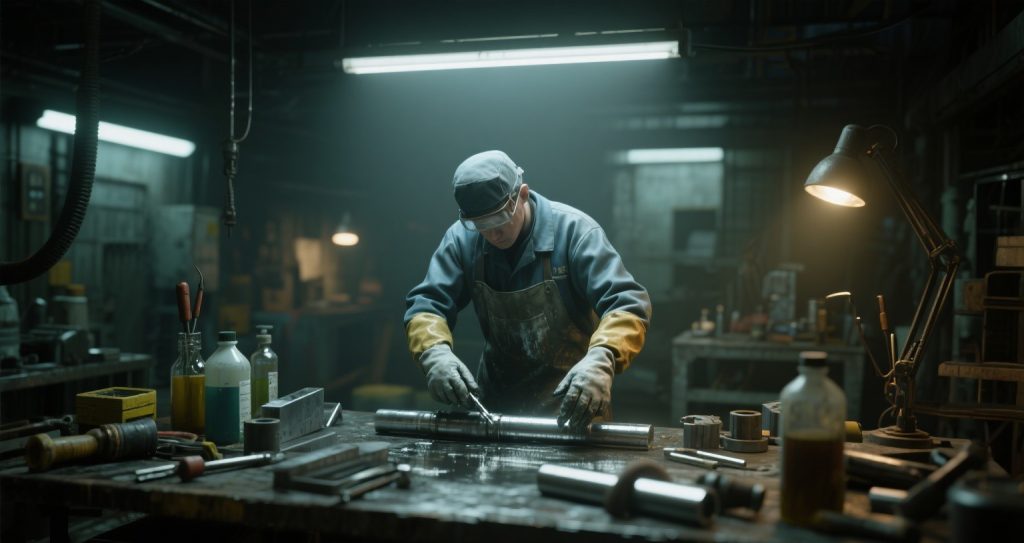
- Post-treatment and Quality Testing
After firing, enamel products may undergo a series of post-treatment processes as needed. For example, some daily-use enamel and artistic enamel products are decorated with color patterns through spraying, decalcomania, printing, etc., to enhance their aesthetic appeal. Industrial enamel equipment undergoes strict quality testing, including appearance inspection (checking for defects such as bubbles, cracks, and peeling), adhesion testing (detecting the bonding strength between enamel and metal through bending, impact, etc.), and corrosion resistance testing (simulating actual use environments to detect the product’s corrosion resistance in acid-base media, etc.). Only products that pass all quality tests can enter the next assembly link or be directly put into the market.
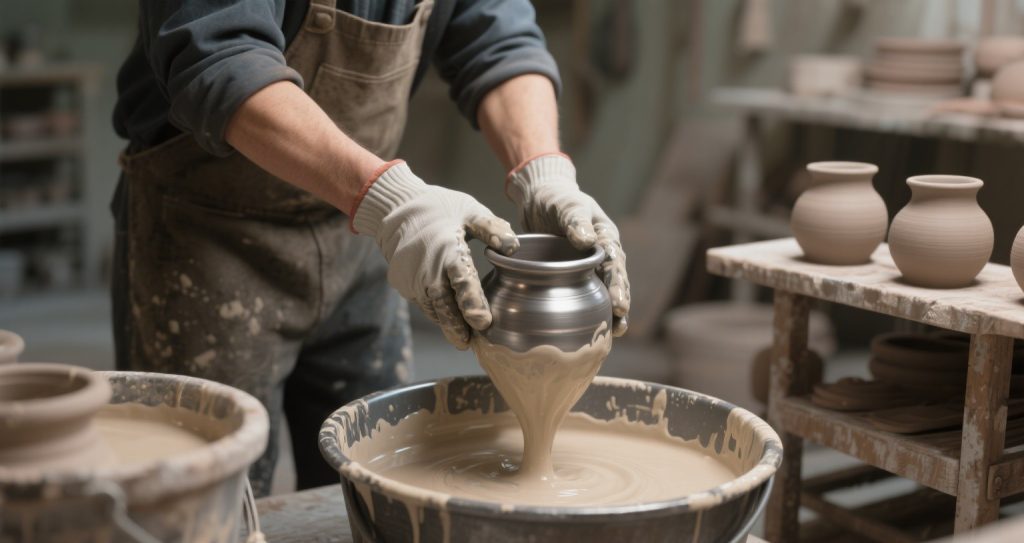
Application Fields of Enamel
- Construction and Decoration Fields
Enamel materials have unique advantages in construction and decoration. Their corrosion resistance, high-temperature resistance, and easy cleaning make them ideal decorative materials for building exteriors. For example, some modern commercial and public buildings use enamel steel plates as exterior wall decorations, which not only exhibit unique colors and luster but also maintain beauty for a long time and reduce maintenance costs. In interior decoration, enamel murals, enamel decorative panels, and other products add an artistic atmosphere to interior spaces with their rich pattern designs and good durability. In addition,with the rise of green building concepts, the environmental performance advantages of enamel materials have enabled them to occupy a favorable position in the competition of new building materials, and the continuous progress of surface treatment technologies can meet the personalized needs of construction and decoration.
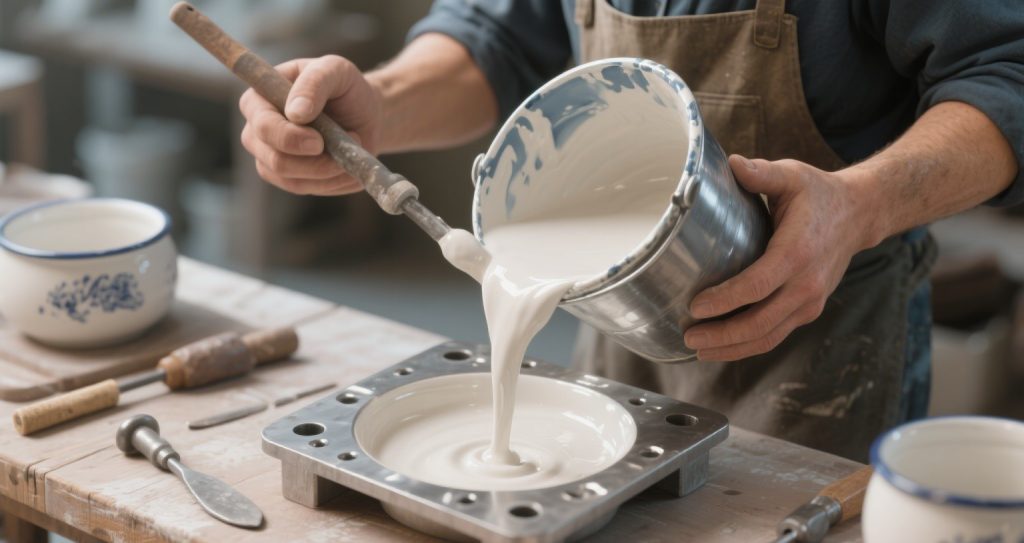
- Home and Daily Necessities Fields
In the home and daily necessities fields, enamel products are ubiquitous. Traditional enamel pots, bowls, basins, cups, etc., were essential household items due to their safety, non-toxicity, and easy cleaning. Today, although many new materials for home supplies have emerged, enamel products still occupy a certain market share with their unique charm. Some high-end enamel kitchenware, through process improvements, have better heat preservation and wear resistance, and more fashionable and beautiful appearance designs, favored by consumers. In addition, enamel vases, handicrafts, etc., combine practicality and artistry, becoming highlights of home decoration.
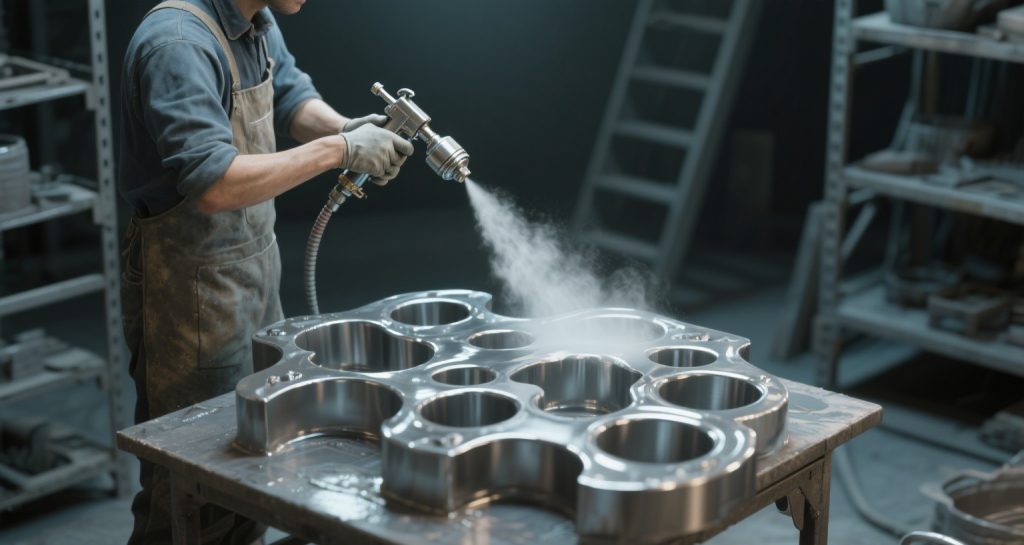
- Industrial Equipment and Chemical Engineering Fields
In industrial equipment and chemical engineering fields, enamel plays an irreplaceable role. Enamel-lined reaction kettles, storage tanks, and other equipment are widely used in petroleum chemistry, food processing, pharmaceuticals, and other industries. Compared with ordinary thin steel plate enamel, glass-lined enamel has a significantly increased silicon content, with properties closer to chemical glass. It can resist the corrosion of various concentrations of inorganic acids, organic acids, weak alkalis, and organic solvents, except for hydrofluoric acid, fluoride-containing media, strong alkalis, and high-temperature concentrated phosphoric acid, which is unmatched by other materials. In the food processing industry, enamel equipment ensures food safety and quality during production due to its non-toxic and hygienic characteristics. In chemical production, its excellent corrosion resistance can effectively extend equipment service life and reduce production costs.
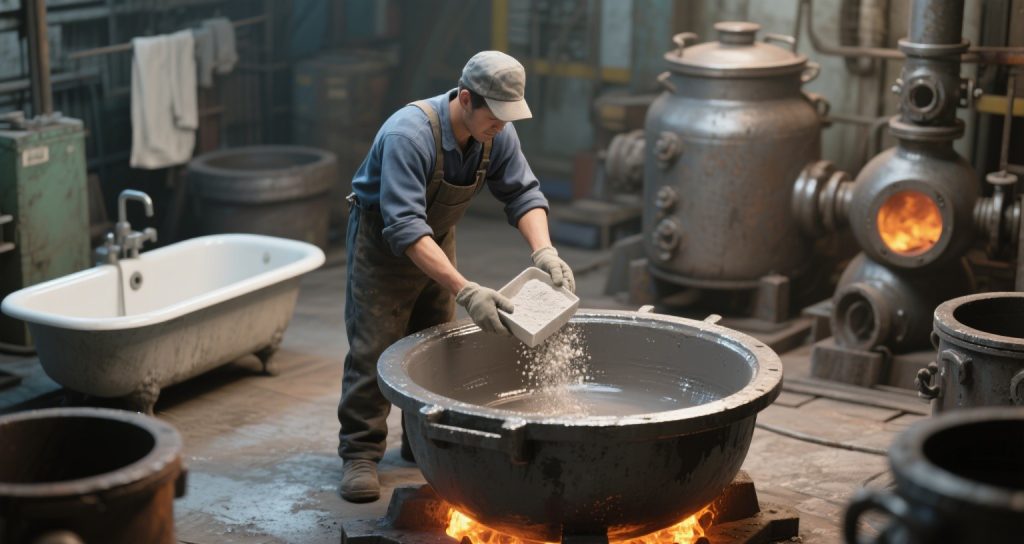
- Medical and Electronic Fields
In the medical field, enamel materials are used to manufacture some medical devices, such as disinfection trays and surgical instrument trays. Their smooth surface, easy cleaning and disinfection, and corrosion resistance help improve the service life and stability of medical devices and reduce medical risks. As medical devices move towards miniaturization and high-endization, the application of enamel materials will become more in-depth. In the electronic field, enamel can be used as an insulating coating for electronic components, using its insulating and high-temperature resistance properties to ensure the safe and stable operation of electronic equipment. For example, in some electronic devices working in high-temperature environments, enamel coatings can effectively prevent short circuits of electronic components and improve equipment reliability.
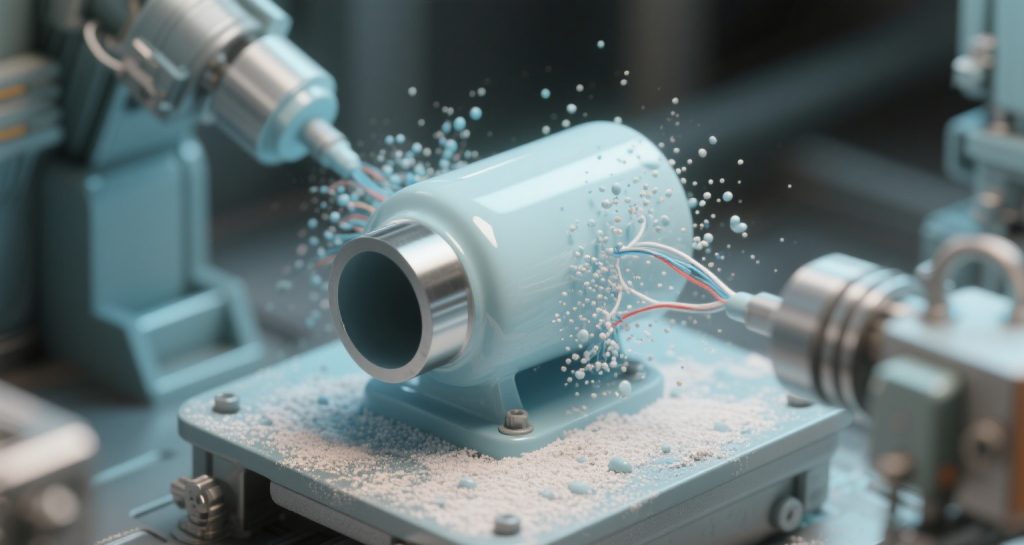
Current Status and Challenges of the Enamel Industry
- Market Landscape and Competitive Situation
Currently, the global enamel market presents a diversified competitive landscape. Internationally, developed countries in Europe and America have an early start in the enamel industry, mature technology, and a number of well-known enamel enterprises, showing strong competitiveness in high-end products and advanced technologies. For example, enamel bathroom products from Germany, Italy, and other countries enjoy a high reputation in the global market for their exquisite craftsmanship and high quality. In developing countries, with the rapid economic development and acceleration of industrialization, the demand for enamel products is continuously growing, and local enamel enterprises are also rising. Relying on cost advantages and understanding of the local market, they occupy a certain share in the mid-to-low-end product market. In China, after years of development, the enamel industry has formed a relatively complete industrial chain, with a large number of enterprises, but the industry concentration is low, and market competition is fierce. Some enterprises have gradually improved product added value and market competitiveness through technological innovation and brand building, and began to move towards the high-end market.
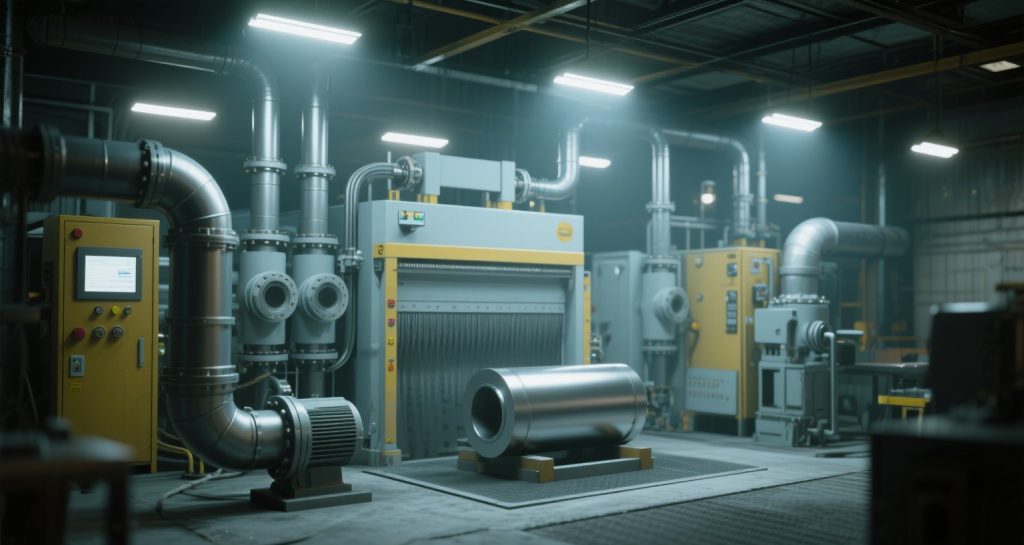
- Bottlenecks in Technological Innovation
Although the enamel industry has made remarkable progress in the past, it still faces some bottlenecks in technological innovation. On the one hand, the research and development of new enamel materials is quite difficult. Although the market has an urgent demand for new enamel materials with higher corrosion resistance, wear resistance, heat resistance, and green, environmentally friendly, and recyclable characteristics, the R&D process requires significant investment in funds, manpower, and time, and involves interdisciplinary collaboration in materials science, chemical engineering, and other fields, with relatively slow progress currently. On the other hand, in terms of production technology integration, although some enterprises have begun to introduce automated and intelligent production equipment, the overall intelligence level of the industry still needs to be improved. The application of technologies such as the Internet of Things (IoT) and big data analysis in the enamel production process is not deep enough, failing to fully achieve production process optimization and full-process quality traceability, thus limiting the improvement of production efficiency and product quality stability.
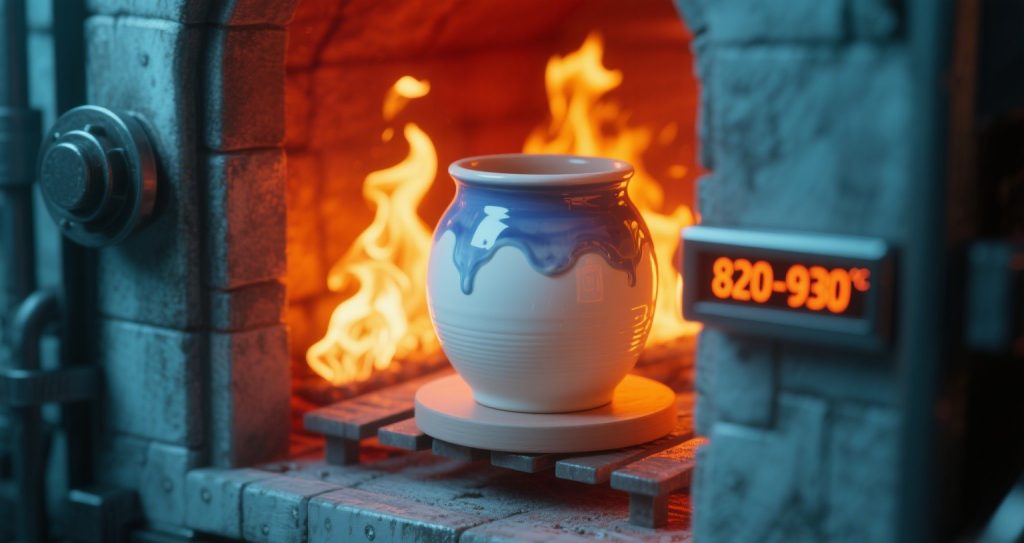
- Environmental Pressure and Countermeasures
With the continuous enhancement of global environmental awareness and the increasing strictness of environmental regulations, the enamel industry faces enormous environmental pressure. In the enamel production process, certain pollutants such as waste gas, wastewater, and waste residue will be generated. For example, traditional enamel formulations may contain heavy metal elements such as lead and cadmium, posing environmental pollution risks during production and use; fuels used in the firing process generate air pollutants such as nitrogen oxides. To address environmental pressure, enterprises need to increase investment in environmental protection, adopt green manufacturing processes, such as promoting the use of clean energy to reduce pollutant emissions in the production process; optimize production processes to reduce waste gas and wastewater emissions and achieve clean production; research and develop green and environmentally friendly enamel materials, such as low-lead and lead-free enamel products, to meet market demands and environmental requirements. At the same time, enterprises must establish a sound environmental management system, improve resource utilization efficiency, and actively respond to national energy conservation and emission reduction policies.
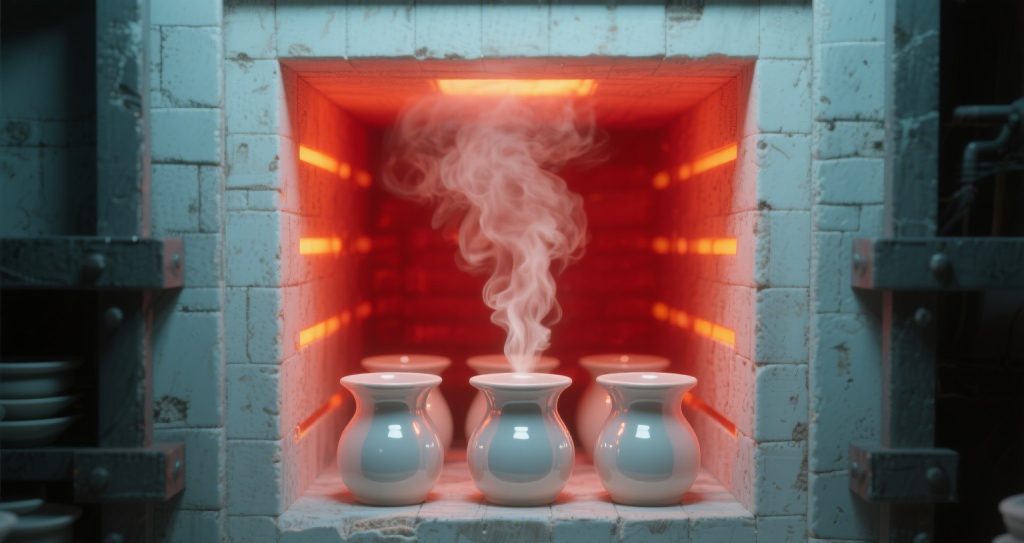
Future Development Trends of the Enamel Industry
- Green Manufacturing and Sustainable Development
Green manufacturing will become the core development direction of the enamel industry in the future. Enterprises will pay more attention to the green environmental protection of the entire life cycle from raw material selection and production process optimization to product recycling. In terms of raw materials, the R&D and application of new green, environmentally friendly, and recyclable enamel materials will be increased, reducing the use of environmentally harmful substances. In the production process, energy consumption and pollutant emissions will be further reduced through technological innovation and equipment upgrading to achieve clean production. Meanwhile, the concept of circular economy will be more widely applied in the enamel products manufacturing industry. By establishing a perfect product recycling system, resource recycling will be realized, waste generation will be reduced, and the industry will be promoted to transform towards sustainable development.
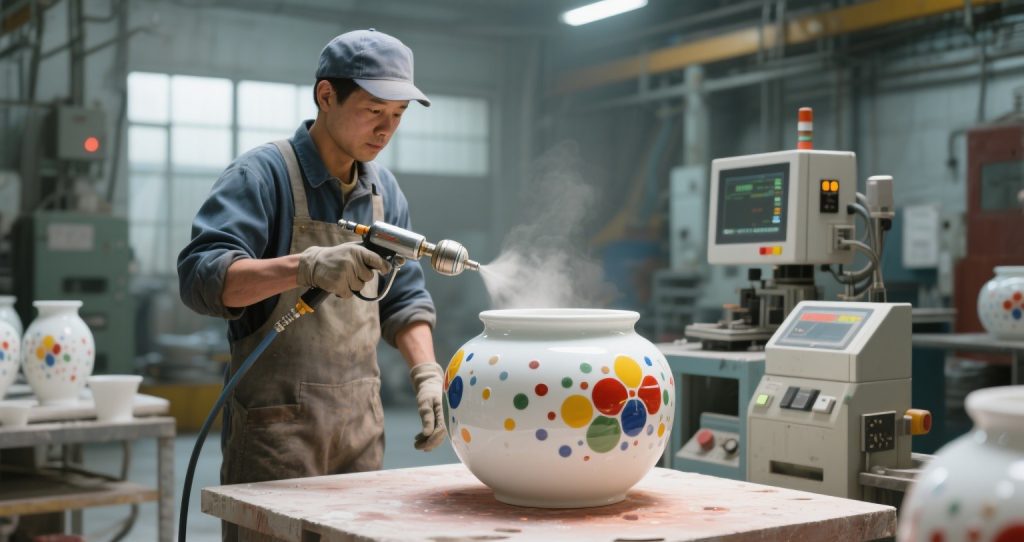
- Intelligent Manufacturing and Digital Transformation
Intelligent manufacturing and digital transformation will profoundly change the production mode and management method of the enamel industry. In the future, enterprises will widely apply advanced equipment such as industrial robots and automated production lines to achieve a high degree of intelligence and automation in the production process, improving production efficiency and reducing labor costs. At the same time, technologies such as the IoT, big data analysis, and artificial intelligence (AI) will be deeply integrated into all links of enamel production. Through IoT technology, interconnection and information sharing among production equipment will be realized, and the production process will be monitored in real time; using big data analysis technology, production data will be deeply mined and analyzed to optimize production processes and improve product quality; with the help of AI technology, intelligent decision-making and fault prediction in the production process will be achieved, further enhancing production stability and reliability. In addition, digital management systems will realize end-to-end digital management from raw material procurement to product sales, improving enterprise operation efficiency and management level.
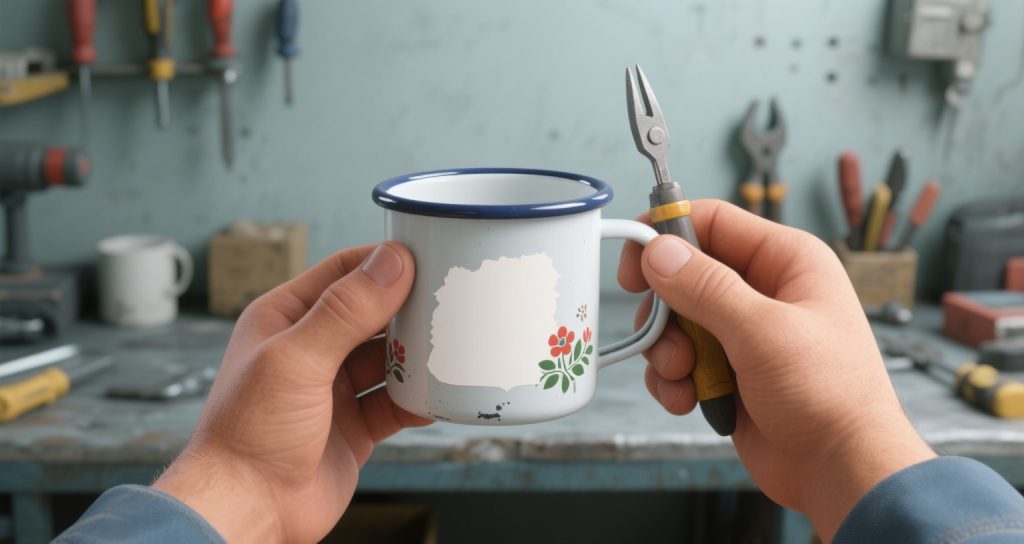
- Product Diversification and Functional Expansion
With the continuous change of market demand and consumers’ pursuit of quality of life, enamel products will develop towards diversification and functionality. In terms of product types, in addition to traditional household items and industrial equipment, more novel products will emerge, such as intelligent enamel home appliances, enamel medical supplies with antibacterial and antiviral functions, and enamel components suitable for new energy vehicles. In terms of product functions, enamel will continue to integrate new technologies and materials to develop products with more special functions, such as self-cleaning enamel, thermal insulation enamel, electromagnetic shielding enamel, etc. Through product diversification and functional expansion, the personalized needs of different industries and consumers will be met, further expanding the market application space of enamel products.
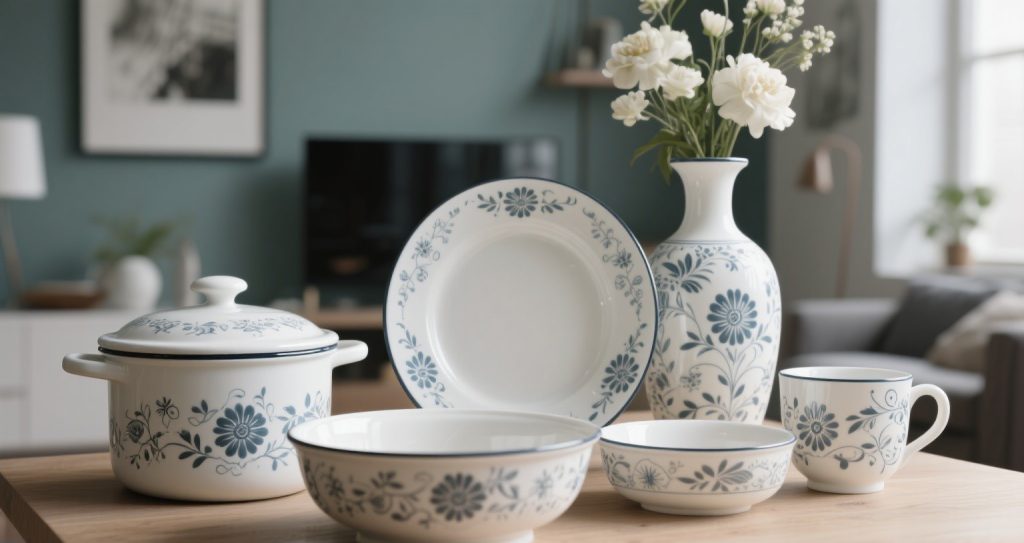
- Cross-Industry Integration and Innovative Development
In the future, the enamel industry will strengthen cross-industry integration with other sectors. Through cooperation with new materials, new energy, electronic information, biomedicine, and other industries, more new products and applications will be created. For example, combining with nanotechnology to develop high-performance enamel products with nanocoatings to enhance surface properties; cooperating with the new energy industry to apply enamel materials to solar water heaters, energy storage equipment, and other fields. In addition, with the development of 3D printing technology, its application in the enamel field will gradually increase. Through 3D printing, personalized custom production of enamel products can be realized to meet consumers’ needs for unique products, injecting new vitality into the innovative development of the enamel industry.
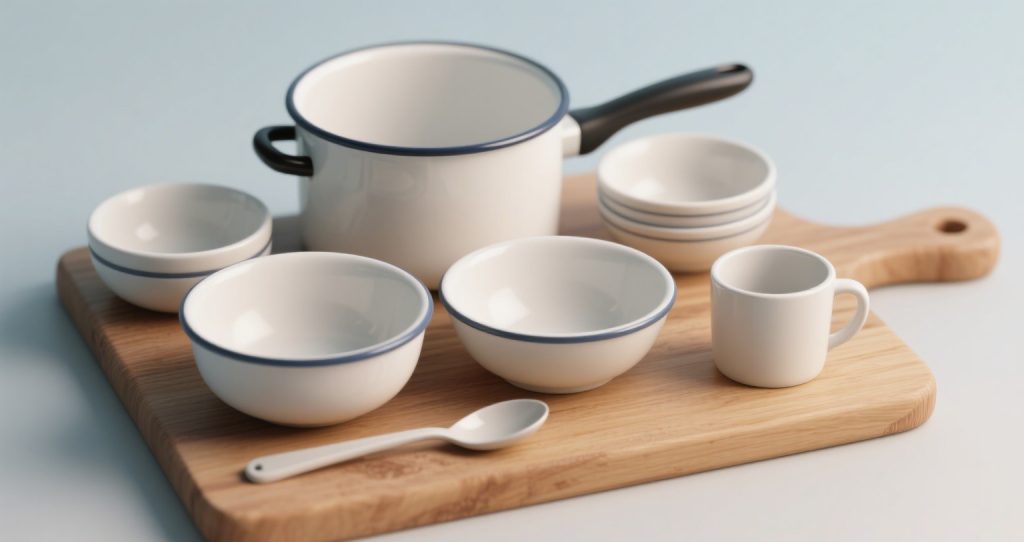
Conclusion
As a traditional industry with a long history, the enamel industry still plays an important role in modern society and shows broad development prospects. Although currently facing many challenges such as technological innovation and environmental pressure, with the continuous development and application of emerging technologies and concepts such as green manufacturing and intelligent manufacturing, as well as the continuous promotion of market demand, the enamel industry is in a critical period of transformation and upgrading. By strengthening technological innovation, promoting green development, expanding product application fields, and enhancing cross-industry integration, the enamel industry will surely achieve sustainable development in the future, continuously providing more high-performance, high-quality, and diversified products for people’s lives and industrial production, and radiating new vitality in the new era.